為什麼在能源轉換市場選擇台灣柏朗豪斯特?
我們提供精確的低壓降氫氣流量測量和控制,真實氣體氫氣校準高達 200 m3n/h,以實現最佳精度。在電池生產中,我們的整合給料功能可確保快速、高精度地分配液體(例如電解液質),從而提高製造製程的效率和精度。
為什麼在能源轉換市場選擇台灣柏朗豪斯特?
我們提供精確的低壓降氫氣流量測量和控制,真實氣體氫氣校準高達 200 m3n/h,以實現最佳精度。在電池生產中,我們的整合給料功能可確保快速、高精度地分配液體(例如電解液質),從而提高製造製程的效率和精度。

廣泛的產品範圍
我們提供各種熱旁路質量流量計和控制器,包括容量高達10,000 ln/min的整合控制器,確保為各種應用提供多功能解決方案。
靈活的研發支援
我們的解決方案專為研發而量身訂製,可透過Bronkhorst FlowSuite 手機應用程式或軟體輕鬆配置,提供靈活性和便利性。
高速精確給料
我們的液體流量控制器具有獨特的整合式高速精密計量軟體,可在液體分配方面提供卓越的準確性和效率。
適用於能源轉換市場的產品
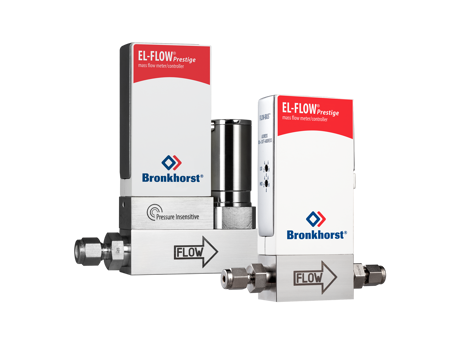
EL-FLOW Prestige
用於氣體的高端質量流量計/控制器
適用於 0.014 mln - 100 ln/min
精確度 *****
內建 100 種氣體的氣體資料庫
適用壓力高達 100 bar
檢視範圍
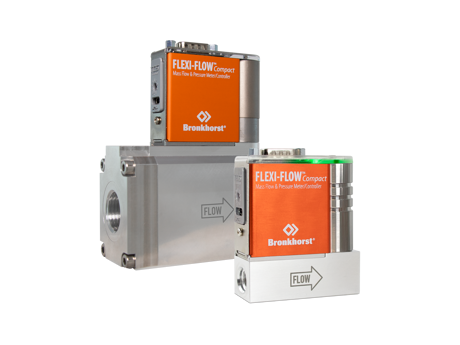
FLEXI-FLOW Compact
氣體用多參數質量流量計/控制器
適用於 0-500 ln/min 和 0-16 bar
精度 ****
內建 22 種氣體的氣體資料庫
多重控制功能
檢視範圍
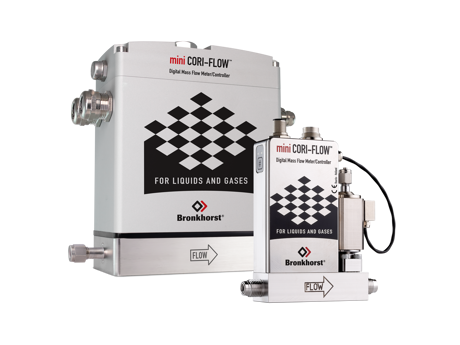
mini CORI-FLOW
適用於液體和氣體的寇里奧利質量流量計,帶控制器輸出
適用於 0...300 kg/h
精確度 *****
最佳配料解決方案
適用於任何流體
檢視範圍
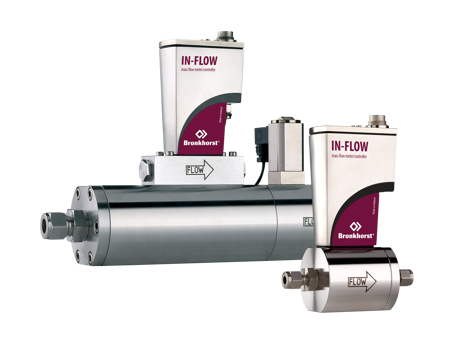
IN-FLOW
IP65 氣體質量流量計/控制器
適用於 0.014 mln/min 至 11,000 m3n/h
精確度 ****
多氣體/多範圍功能(選配)
適用壓力高達 700 bar
檢視範圍
尋找解決方案
為您的氣體、液體、蒸氣或壓力應用尋找合適的儀器。透過我們廣泛的產品系列,我們將協助您找到符合您需求的產品。現在就開始探索,發現您理想的解決方案。

